Brief
« Nous avons l’usine de démantèlement automobile la plus technologique du monde – il faut que ça se voit ! »
Chaque année en France, environ 1.5 million de véhicules deviennent hors d’usage. Le métier de GPA est de les collecter et de donner une seconde vie aux pièces et matières qui les composent, tout en recyclant leurs produits polluants.
Johan Renaud, dirigeant de l’entreprise, souhaite équiper la nouvelle ligne de production de pupitres de commande pour chaque étape du démontage. Le pupitre intègre l’interface de travail des opérateurs et les commandes des machines spéciales utilisées pour dépolluer les véhicules, les lever et les faire avancer.
Au-delà de la fonction technique, le pupitre sera aussi un vecteur d’image pour cette usine de pointe dans son domaine.
L’agence Entreautre et le 8fablab associent leurs compétences pour répondre au besoin de GPA avec l’ambition de livrer 35 pupitres opérationnels pour la mise en route de l’usine. Une équipe interne à GPA est également mise en place pour piloter et participer au projet (maintenance, informatique, industrie, opérateur).
Analyse des besoins
Analyse des besoins utilisateurs
Une immersion sur le site de production est le meilleur moyen de comprendre les besoins. La visite de l’ancien site de démantèlement est l’occasion d’observer les façons de travailler et d’échanger avec les opérateurs. Autant de données précieuses pour documenter notre analyse et définir les fonctions du produit.




3 grandes fonctions indispensables :
- Centralisation de l’ensemble du matériel utilisé sur les postes
- Facilitation de la communication interne entre les différents opérateurs du site
- Être un marqueur de l’entreprise à des fins de communication externe
Simplicité et efficacité guident notre travail de conceptualisation.
Le pupitre est avant tout un outil de travail du quotidien pour les opérateurs de production.
Il faut y intégrer leurs outils informatiques, outils de communication, outils à main… et des commandes spécifiques à chaque machine.
Design produit
Nous dessinons des objets et produits pour qu’ils soient fabriqués le plus simplement possible
Les premiers coups de crayons nous orientent sur l’architecture et le mode de construction des pupitres. Nous utiliserons de la tôle d’acier peinte parce que c’est structurant, résistant et accessible. Nous avons des partenaires locaux pour la production – la découpe laser et le pliage offrent quelques libertés de formes.

Sur une base d’une structure commune, nous déclinons des variantes du pupitre en fonction des postes de travail.
Une logique de système d’objets qui permet de faire des économies d’échelle sur la production et de donner une cohérence d’ensemble aux pupitres.
Conception mécanique et intégration technique
Nous travaillons main dans la main avec l’équipe du 8fablab. Sur la base du concept d’architecture produit, Bastien (concepteur mécanique) et Théo (ingénieur électronique) conçoivent l’intégralité du système.
Le pupitre est un mobilier “actif”. Il intègre de nombreuses prises de courants utiles pour brancher tous les équipements embarqués. Il dispose aussi d’un système de communication à 3 boutons – spécifique à la ligne de production GPA – dont un dédié à l’entraide entre les opérateurs. Nous passons du temps à trouver les bons composants (sourcing) et à les intégrer dans le pupitre.

Prototypage
Avec Tolerie Metal Indus, à Bourg-de-péage, nous réalisons le prototype du pupitre. Il nous sert à faire les dernières mises au point techniques avant la production en série.






Industrialisation
Un projet mené en 5 mois de l’idée à la série opérationnelle sur site.
Un produit identitaire pour GPA et une ligne de production remarquable.
Un démarche de co-design depuis l’identification du besoin jusqu’à l’industrialisation
La visite du site quelques mois après l’installation, confirme le succès du projet. L’appropriation par les équipes est totale – les pupitres ont même été customisés pour porter pelles et balais….
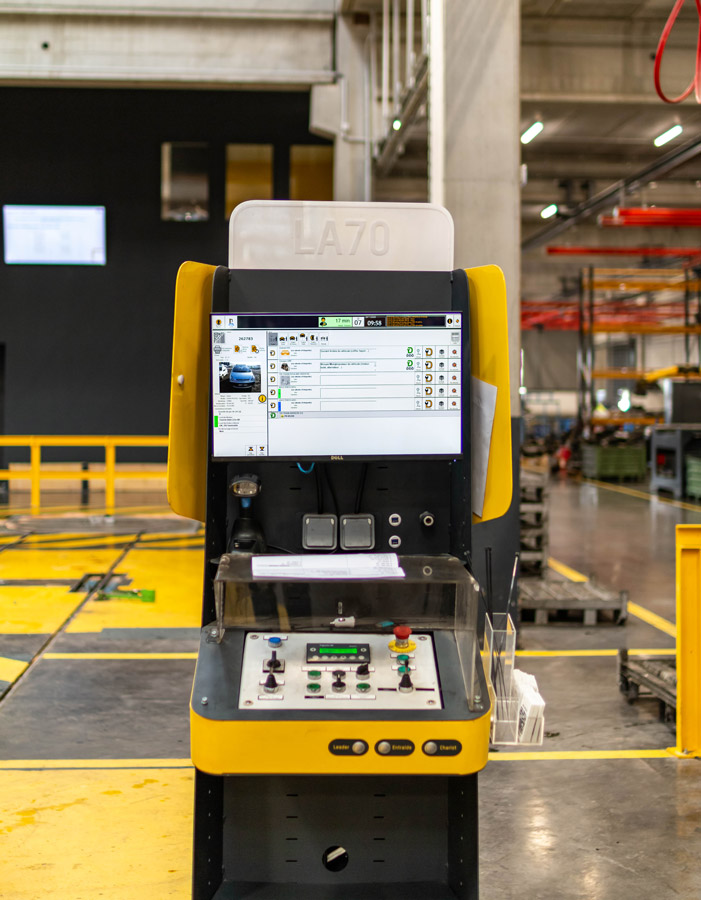

